TDI/MDI DETECTION BADGES
– TDI/MDI CHEMICAL DETECTION DEVICES
DETECT TDI/MDI ON THE JOB SITE
Aromatic diisocyanates, such as toluene diisocyanate (TDI) and methylene diphenyl diisocyanate (MDI), are commonly used to make polyurethane foams and related products. Inhalation of these diisocyanates can lead to irritation or damage to the respiratory track.
SafeAir TDI/MDI badge is a simple, cost-effective, industry-proven solution for TDI detection and/or MDI detection in the workplace. The badge uses colorimetric technology (i.e. color change) to provide immediate indication when TDI/MDI vapor is present. No need for lab analysis or electronic reader.
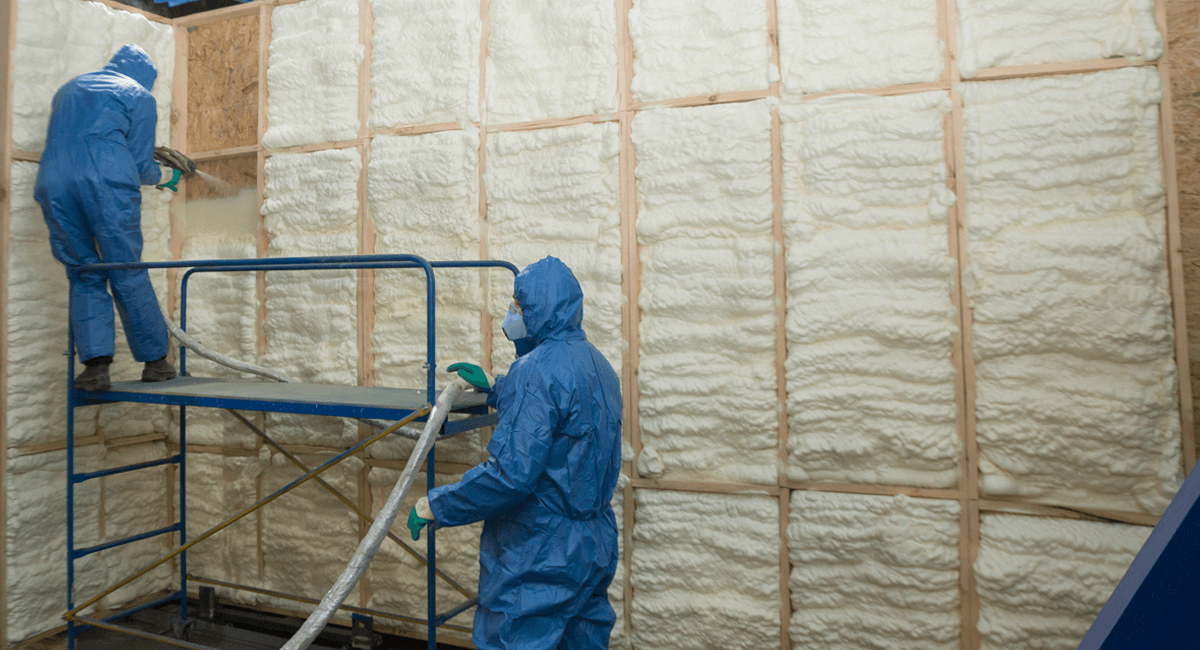
– PRODUCT DETAILS
SafeAir TDI/MDI Badge (Part#: 382001)
SafeAir TDI/MDI badge provides an immediate visual indication of exposure to TDI/MDI. When TDI/MDI vapor is present, the exclamation mark in the triangular window changes color. The intensity of the color change is proportional to the exposure dose. SafeAir TDI/MDI badge is a simple, cost-effective solution for TDI/MDI detection in the workplace.
Click here for operating instructions for SafeAir TDI/MDI detector badges.
Employee Monitoring
An employee wears badge near their breathing zone
Leak Detection
Place badge near the source of potential leak
** Badge Clips Sold Separately.
The comparator is used to determine TDI exposure dose by matching the color on the badge to a color on the comparator color wheel. It measures TDI exposure dose from 5 to 140 ppb-hour.
View the video for instructions on how to use the comparator.

SafeAir MDI Color Comparator (Part#: 383006) is an optional accessory for use with SafeAir TDI/MDI badge (Part# 382001). Badges are sold separately.
The comparator is used to determine MDI exposure dose by matching the color on the badge to a color on the comparator color wheel. It measures MDI exposure dose from 5 to 140 ppb-hour.
View the video for instructions on how to use the comparator.

BY PHONE:
+1-757-431-2260
E-MAIL:
For customers outside the US, email or call to be referred to a distributor.
Available on Amazon (for US customers)
Available on GSA (for US government customers)
GS-07F-0147T (Laurus Systems, Inc.)
– Frequently Asked Questions –
FAQ
Where is TDI/MDI Used?
Aromatic diisocyanates, such as toluene diisocyanate (TDI) and methylene diphenyl diisocyanate (MDI), are commonly used to make polyurethanes and related products. Polyurethanes have significant application in the manufacture of rigid and flexible foams. Diisocyanates are also used in the production of adhesives, elastomers and coatings.
What are the health effects of TDI/MDI exposure?
Inhalation of aromatic diisocyanates can be a respiratory irritant, and dermal exposure can be a skin irritant. Chronic overexposure has also been reported to cause lung damage including fibrosis. Aromatic diisocyanates such as TDI and MDI have also been shown to be respiratory sensitizers, which causes certain individuals to become more sensitive to exposure. Repeated exposures or a single large dose may cause sensitization.
What are the exposure limits for TDI/MDI?
OSHA and NIOSH exposure limit for TDI is 0.02 ppm (TWA), the OSHA exposure limit for MDI is 0.02 ppm (ceiling) and the NIOSH exposure limit for MDI is 0.005 ppm (TWA). The Occupational Safety and Health Administration (OSHA) in the United States implemented a National Emphasis Program in 2013 to protect workers from the serious health effects from occupational exposure to isocyanates, such as TDI and MDI.
How does a TDI/MDI badge change color?
A color-forming reaction occurs when TDI or MDI reacts with the proprietary indicator layer in the SafeAir TDI/MDI detector badge.
What types of Polyurethane (PU) Products are made from TDI and MDI?
Note: ADI means aliphatic diisocyanate
How is the Chemical Industry Involved with Isocyanate Safety?
The chemical industry is active in promoting the safe use of isocyanates. Many chemical companies have product stewardship programs to help their customers ensure a safe work environment for their employees.
The American Chemistry Council (ACC) provides information on the safe use of isocyanates in the workplace, including air monitoring of isocyanates.
Isocyanate producers are often members of the International Isocyanate Institute (III), whose principal aim is to promote the safe handling of MDI and TDI, with respect to the workplace, the community and the environment.
ISOPA is the European trade association for producers of aromatic diisocyanates and polyols – the main building blocks of polyurethanes. ISOPA is a partner association of the European Chemical Industry Council (CEFIC) and the ISOPA members include BASF, BorsodChem, Covestro, Dow, Huntsman and Shell Chemicals. ALIPA is the European Aliphatic Isocyanates Producers Association. It was created by the major European producers BASF, Covestro, Evonik and Vencorex. Both ISOPA and ALIPA encourage the safe and proper use of isocyanates and promote the highest level of best practices in the distribution and use of diisocyanates and polyols in Europe and ensures that all stakeholders can easily access accurate and up-to-date information on these substances.
Companies which make or use isocyanates often use SafeAir TDI/MDI badges in conjunction with area TDI detectors and/or area MDI detectors.
What are the REACH Restrictions for TDI/MDI?
On 4 August 2020, the REACH Restriction on diisocyanates was published in the EU official journal applying after a transition period of three years. The Restriction introduces mandatory training requirements for workers using and handling diisocyanates and mixtures containing diisocyanates. REACH places the burden of proof on industry. To comply with the Regulation, companies must correctly identify and manage risks. In turn, chemical producers must demonstrate to the European Chemicals Agency (ECHA) how a substance can be safely used and communicate any risk management measures to their users. The REACH restriction on diisocyanates outlines the training materials and courses that suppliers of diisocyanates and diisocyanate containing mixtures must provide to their employees and customers. The training shall take into consideration the specificity of the products supplied, including composition, packaging, and design, and will be conducted via in person or online class by accredited trainers. Users are responsible for documenting the completion of their training and for renewing their training certification every 5 years. EU Member States must report on their established training requirements, the number of reported cases on occupational asthma and occupational respiratory and dermal disease, any national occupational exposure levels and information on enforcement activities directly to the ECHA. Industry professionals must be fully prepared, trained, and compliant by August 24 2023. Member companies of ISOPA and ALIPA as are working closely together to develop the required set of training.
– DETECT TDI/MDI & OTHER TOXIC CHEMICALS
ADDITIONAL CHEMICALS
- GET IN TOUCH -