Ammonia
In our last segment of the Ammonia blog series, we discussed what ammonia is, how it is used and where. We shared characteristics that showcase the good and bad of ammonia use and production. This article intends to share the history of ammonia and what its current production looks like. Further insights on the evolving landscape of clean ammonia and will take place in the upcoming series articles.
An Ammonia review:
Ammonia is found in industries like fertilizer production, industrial refrigeration, and chemical manufacturing. It is so widely used due to its versatile reactivity that stems from its basic properties, ability to form hydrogen bonds and ligand characteristics. Ammonia, although extremely useful, is also a threat to individual health and its safety is top of mind for many. When exposed to ammonia in large quantities, individuals may have a range of health effects from irritation of the eyes, nose, or throat to more serious injuries like burns and blisters or pulmonary edema. SafeAir and ChromAir chemical detection badges and similar products were developed to increase workplace safety while monitoring individuals and areas for potential exposure below or at the OSHA and NIOSH exposure limits (listed below).
NIOSH REL | TWA 25 ppm (18 mg/m3) ST 35 ppm (27 mg/m3) |
OSHA PEL | TWA 50 ppm (35 mg/m3) |
Ammonia in Nature
Ammonia is a naturally occurring chemical that can be found in nature abundantly. The process of natural occurrence is derived from the decomposition of plant and animal waste. Ammonia is naturally found in soil, water, and air.
Where it all started
Before we look to the future of ammonia and ongoing efforts to bring ammonia into the “Clean Chemistry” space let’s first discuss the history of ammonia. About a century ago a German Chemist, Dr. Fritz Haber, developed a method to producing ammonia. This method was efficient and would eventually lead to the inexpensive manufacture of ammonia and significant increase in its availability. The process described below accounts for nearly 98% of ammonia production. As a result of this efficient method, the subsequent increase in agriculture production (through fertilizer) that has allowed the world’s population to flourish. Ammonia’s primary means of production from nearly the full century since developed, has been the Haber-Bosch process.
The Haber-Bosch process was developed by Dr. Fritz Haber – in an attempt to establish an efficient process for generating ammonia. Ammonia is used in a variety of different applications including fertilizers and explosives. Haber’s discovery of the efficient mixing of hydrogen and nitrogen gas under specific circumstances set the stage for Karl Bosch’s contribution. Also a German Chemist, Bosch commercialized the ammonia production process a few years after Haber’s initial discovery.
The Haber-Bosch Method
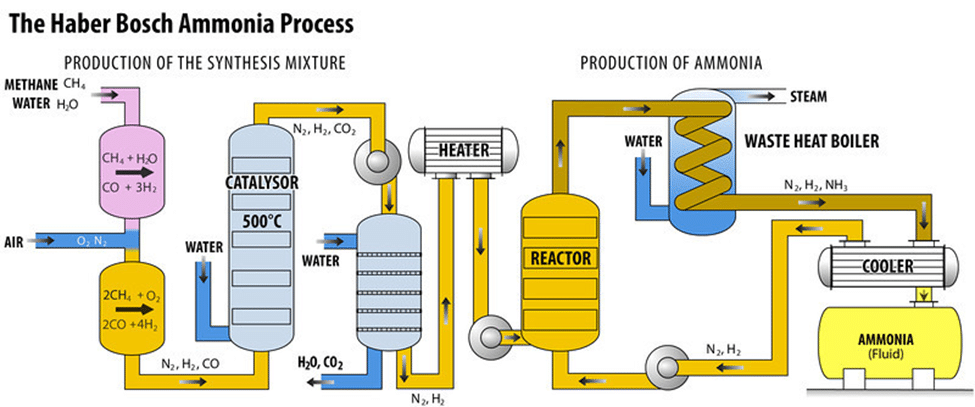
Conditions:
The Department of Physics at Stanford University describes the requirements for the Haber-Bosch method below:
“The required reaction conditions for the Haber-Bosch process make it very energy-intensive. In the ammonia-production stage, hydrogen and ammonia react at 15-25 MPa and 400-450 degrees Celsius with a typical iron-based catalyst. [1] These high temperature and pressure conditions require a large input of energy and are part of the reason why the actual Haber-Bosch energy consumption, 11.90 EJ, deviates from the theoretical minimum, 0.15 EJ, calculated at ambient conditions. The theoretical minimum is also assuming 100% conversion from reactant to product, which is often not the actual case. Finally, the theoretical minimum does not account for any cost from separating the ammonia from other products and reactants.”
History of Ammonia Conclusion
As we’ve seen, ammonia has played a crucial role in shaping modern industry and agriculture, with the Haber-Bosch process serving as the foundation for its large-scale production. While its benefits are undeniable, ammonia’s widespread use also comes with safety and environmental concerns that cannot be ignored. From its natural presence in the environment to its industrial applications, ammonia continues to be a critical chemical—one that requires careful management and monitoring to ensure both human and environmental safety.
Looking ahead, the conversation around ammonia is evolving. The push for sustainability and cleaner industrial practices has led to innovations in “clean ammonia,” a concept that seeks to maintain ammonia’s benefits while reducing its carbon footprint. In our next article, we’ll explore what clean ammonia is, how it’s being developed, and what it could mean for industries that rely on this essential chemical. Stay tuned as we dive into the future of ammonia and its role in a more sustainable world.